Understanding and Resolving Common S700 Safety Card Errors
20 November, 2024 | Kollmorgen, S700, Safety Card, Errors, How to, ServoStar, Resolving Error, S700 Series, Brake Control, Limited Speed, Safe Stop, Help
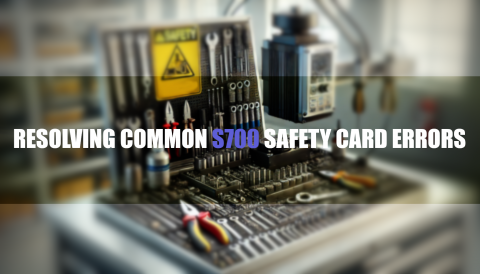
Understanding and Resolving Common S700 Safety Card Errors
As any experienced manufacturer knows, safety cards are the backbone of the S700 servo drive system. When that safety card throws an error, suddenly your entire operation screeches to a halt. And costly downtime starts ticking away by the minute.
Not ideal, to say the least.
Luckily, most safety card errors aren't catastrophic failures. More often than not, they're fairly routine issues that crop up from time to time. With the right knowledge and troubleshooting approach from specialists like Wake Industrial, many can be sent in for repair, resolved quickly, and get shipped back to get production rolling again.
That's where this guide comes in! Below, we'll explore the most common S700 safety card errors for Kollmorgen servo drive, explain what causes them, and detail proven solutions to get your system back up and running.
What is a Safety Card?
First, let's do a quick S700 safety card recap for context.
As mentioned above, the Safety Card S1 module is an essential add-on for the S700 drive. It performs vital safety functions like:
- Safe Stop 1 (SS1): Applies controlled braking ramps to stop motion
- Safe Stop 2 (SS2): Brings motion to a complete stop then disables torque
- Safe Operating Stop (SOS): Stops motion while still allowing low-speed inching
- Safe Brake Control (SBC): Manages motor holding brakes
- Safely Limited Speed (SLS): Monitors max speed limits
Motion Monitoring Errors (Error Index 1-6)
Some of the most frequent errors relate to the safety card's motion monitoring functions while performing controlled stops. For example:
Error 1.1 - Braking Ramp Time Monitoring
This typically crops up if the tolerance window configured for verifying the SS1 braking ramp time is overly tight. For example, normal inertia changes may cause the ramp to take 5-10ms longer than the allowed window.
Potential fixes: Check your configured tolerance value and widen the window if needed to prevent nuisance errors. Our technicians can analyze your ramp profiles and realign for optimized tolerance.
Error 2.1 - Standstill Position Monitoring
Much like the above error, this one indicates the configured tolerance for verifying standstill position after an SS2 stop is too narrow. Normal vibration or settling may cause the stopped position to slightly overshoot the window.
Potential fixes: Review your standstill monitoring tolerance setting and potentially open it up to avoid faulty error triggers while still ensuring safety.
Wake Industrial can help dial-in these key motion monitoring parameters for your specific equipment's normal behavior. Tuning them properly is crucial to maximize safety while avoiding unnecessary nuisance stops.
Brake Testing Errors (Error Index 7)
Because brakes are so vital for stopping vertical axes and heavy loads, brake issues trigger an immediate error event to avoid dangerous failures. For example:
Error 7.1 - Motor Holding Brake Test Failure
This error indicates that when performing the automatic periodic brake tests, the motor holding brake slipped excessively or failed to hold position.
Potential fixes: Verify proper brake wiring, replace worn brake components, increase the brake test current, and confirm proper brake release and activation timing.
Error 7.2 - External Brake Test Failure
Similar to the above error, this means an external supplemental brake slipped or failed testing. Steps to resolve it include:
- Inspect the mechanical brake mechanism for wear or damage
- Check the brake test procedure and current levels
- Verify wiring to the brake solenoid
- Test the brake independently to confirm proper operation
Since brakes are mechanical systems, they naturally wear over time. If slipping becomes chronic, replacement may be necessary.
Input and Output Testing Errors (Error Index 12-13)
Proper functioning of the safety card's inputs and outputs is verified during periodic self-tests. Failures trigger errors like:
Error 12.1 through 12.9 - Safety Input Test Failed
Input test failures commonly indicate wiring disconnections or issues with the input modules themselves. Thoroughly inspect the input wiring for loose connectors, corrosion, or breaks. Also confirm proper module functionality and replace if defective.
Error 13.1 through 13.9 - Safety Output Test Failed
Similarly, output test failures typically stem from wiring faults or module issues. Check for short circuits, bad connections, and proper wire shielding. Swap out external output modules if needed.
Power Supply Errors (Error Index 14)
Reliable power delivery is obviously essential to safety card operation. Insufficient 24V DC supply can lead to events like:
Error 14.1 - Undervoltage
This often results from problems like excessive voltage drop over long power cable runs. It may also indicate failing power supply components. Thoroughly measure voltages throughout the affected circuit. Improve connections, boost power capability, or replace units as needed.
Error 14.2 - Internal Power Supply Failure
This error points to a catastrophic internal safety card power failure. The card will require replacement to restore proper operation. Keep spares on hand for fast swap-out in this situation.
Encoder and Position Monitoring Errors (Error Index 19)
Safety functions depend on accurate and reliable feedback from the motor encoder. Encoder issues generate errors like:
Error 19.5 - Encoder Signal Too Small
This typically results from wiring faults, poor connections, or signal quality issues. Inspect encoder wiring thoroughly and measure signal strength. Replace defective cables or encoder components as needed.
Error 19.9 - Position Jump Detected
Sudden position changes indicate a disconnected or malfunctioning encoder. Again, wiring should be carefully inspected. Also confirm proper mounting, installation, and tensioning of couplings and other mechanical components.
Configuration and Communication Errors (Error Index 28-31)
With the complexity of drive networks, fieldbuses, and configurations, errors can creep in during programming changes and firmware updates:
Error 28.3 - Invalid Safety Card Type
This typically appears if an incorrect or incompatible safety card model is inserted in the drive. Confirm you are using the proper safety card for your S700 series to avoid mismatches.
Error 29.1 - Faulty SD Card
If you're using an SD card to clone configuration settings between drives, this error indicates the card itself has an issue. Try re-formatting the SD card to resolve basic file system problems. If the error persists, replace the damaged card.
Error 31.2 - Safe Torque Off Active
This isn't necessarily a fault itself. But it indicates a loss of communication between the drive and safety card that caused the safety card to disable torque for safety. Check connections and cycling power often resolves temporary communication glitches.
Need Expert Help?
We've covered a ton of ground on the most common S700 safety card errors and proven methods to resolve them. While some may require replacement parts or expert intervention, you now have an invaluable troubleshooting reference to maximize uptime.
Of course, if any safety card issues have you stumped, the team at Wake Industrial stands ready to help with replacement parts, system checkouts, and all of your industrial automation needs. We know how critical it is to minimize costly downtime, so count on our experts for the fastest solutions when safety errors strike.
Contact Wake Industrial today to ask about our comprehensive S700 safety card repair services. We'll get your drive system safely back up and running and shipped out to you in no time!