A Guide to Profibus Communication
7 July, 2020 | Profibus, Communication, Automation System
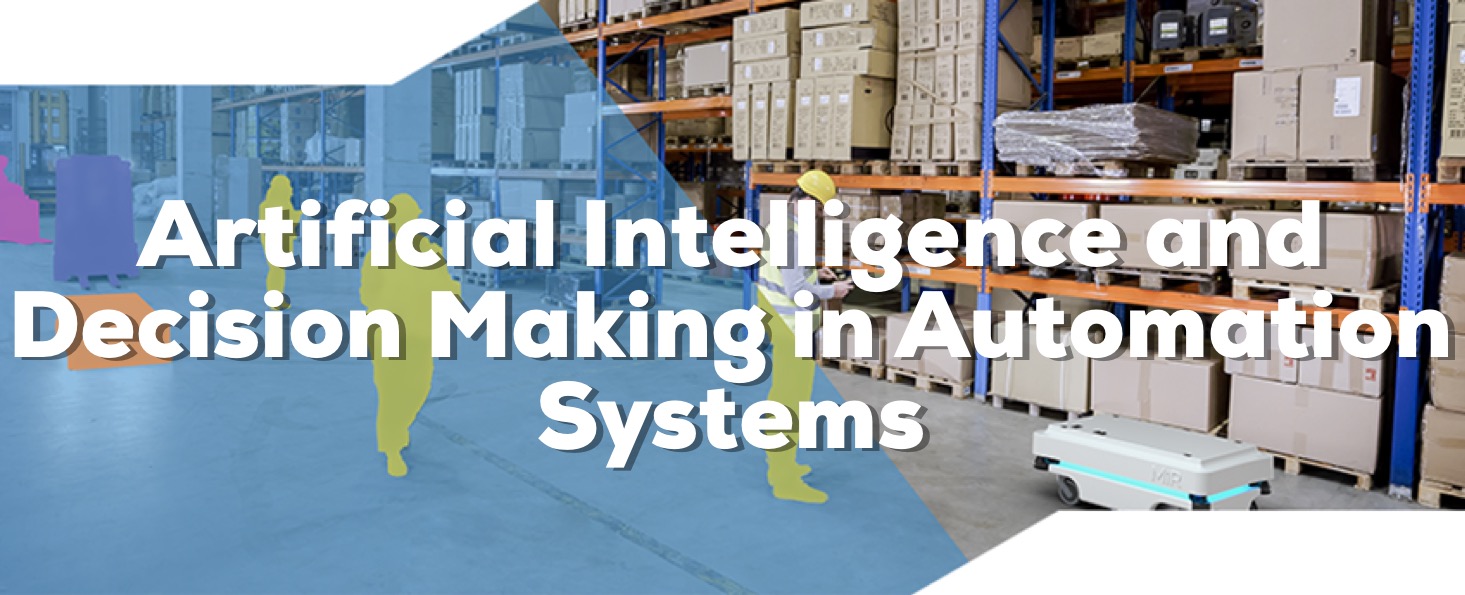
Throughout the years, industrial automation has seen rapid expansion in both technology, scope, and uses. There are now several kinds of automation protocols, all of which have their specific structures and advantages. Profibus communication is among one of the most unique, able to suit a range of specific needs while maintaining a high standard of quality. What exactly is Profibus, though, and what are its benefits? Here’s what you need to know.
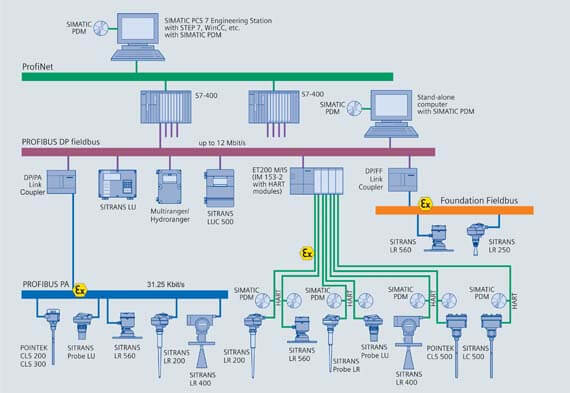
The Basics of Profibus
Profibus was initially designed in the early 1990s to meet industrial communication needs for process automation and factory automation. Rather than being a single standard system, Profibus is a fieldbus-based network standard that consists of a variety of protocols all built on the same technology system. This vast interface can be used and implemented for a wide array of applications and users can combine different varieties of Profibus communication with their own software to create an even more unique application profile. In other words, Profibus is highly flexible, with a “family” of versions providing greater efficiency, better technology, easier maintenance, more streamlined use, and a lower cost for plant managers.
How Exactly Does Profibus Communication Work?
Because Profibus is a smart, fieldbus-based technology, it allows for real-time distributed control. Devices that are part of the system connect with decentralized field devices like sensors and actuators and can then efficiently communicate information with higher-ranking systems through automated messages. However, this communication system can also do a lot more, participating in self-diagnostic processes, connection diagnosis, and more.
Should any of these processes and data exchanges go wrong, though, all joined devices are a little more protected than those that are part of the more traditional Modbus protocol. This increased protection is because each connection, or slave, maintains a failsafe counter. Should the master not communicate with it promptly, the slave then enters a safe state and will only come out of it after the master goes through the startup sequence again. Thanks to this, all communication during each bus cycle will happen with a specified time value.
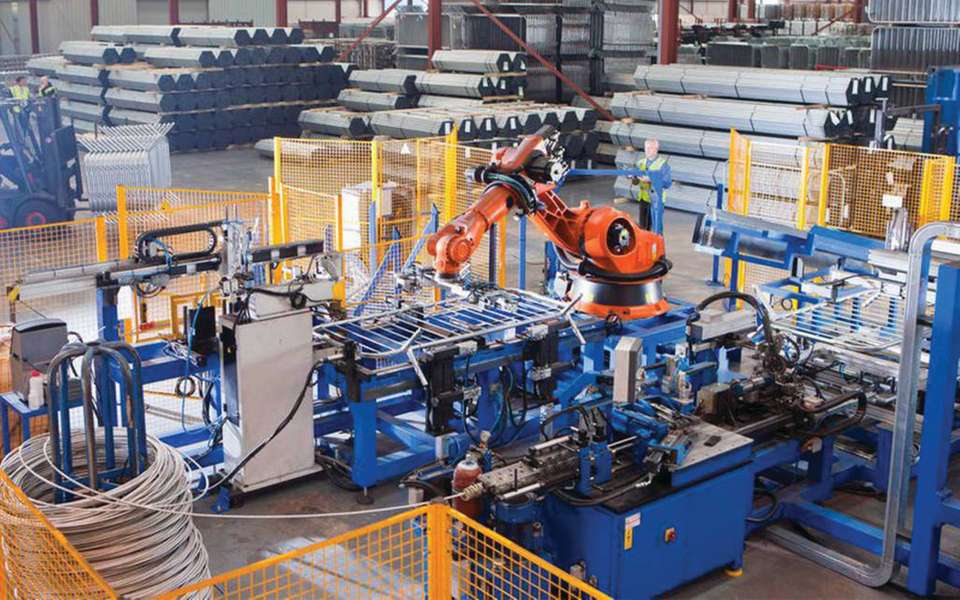
The Different Types and Applications of Profibus
Since Profibus communication isn’t one set system, it advances and changes as needed. Over time, it has gone through a few sets of revisions, with some developing into an entirely new/different Profibus set. Now three main compatible versions exist including:
- Profibus-FMS: The original version of Profibus, Profibus-FMS, or Fieldbus Message Specification, was designed to connect and send complex information between PCs and programmable controllers. Unlike later versions of Profibus, this protocol was unfortunately not nearly as flexible and found itself inappropriate for both simpler messages as well as communications on a more expansive network. While it’s still available today, these disadvantages still plague it. These issues have led to it falling out of favor with a majority of users, who now tend to opt for newer, more suitable solutions.
- Profibus-DP: A more universal protocol than the ones that came before it, Profibus-DP, or Decentralized Periphery, is one of the most used today. It is simpler, faster, and more powerful, allowing users to combine requirements for a more specific solution. This is further helped by the fact that Profibus-DP itself has three separate versions, which allow for greater complexity and newer features.
- Profibus-PA: Profibus-PA was designed for process automation and standardized the process of measured data transmission. It finds particular use within hazardous environments since it is often used in conjunction with Manchester Bus Powered technology to step the power down and reduce the risk of sparks or full explosions. Despite its specific protocol, Profibus-PA isn’t exactly an entirely different type of Profibus. Instead, it’s more so a unique type of Profibus-DP application.
With these three Profibus types, they can find wide applications throughout various industrial processes. They close the gap of digital communication for automation systems and essentially allow the automation of entire plants.
Both big and small plants, factory automation and process automation, and local and remote sections are all covered under Profibus’ adaptable technology. Ultimately, this means that there are better diagnostics, plant design is simplified, data to operations or management staff is faster, faster commissioning is allowed, and costs can go down while productivity goes up.