Okuma's Japanese Dream Site Facility
15 February, 2019
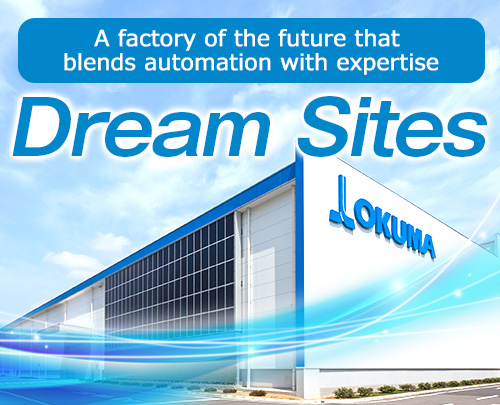
Okuma Automation, renown worldwide for their huge role in industrial CNC machines and milling centers, is building a new product manufacturing facility. However, this facility is like no other Okuma production facility. Okuma’s operations department has completely revolutionized the way Okuma will make their products by implementing numerous robotic systems and automated gear, cutting production times and increasing total volume output of the Japanese plant in Oguchi. Covering 254,000 square feet, the plant is Okuma’s “dream site” for manufacturing production of their high-end CNC Lathes and systems. The plant, by itself, is capable of producing more than twice the total volume in half of the amount of time as the Okuma facility it is replacing.
Okuma is building this facility to stay competitive in a variety of markets tailoring to both mass producers and specialized machine shops. They have expanded their current product line because of an all new flexible manufacturing setup on the plant floor. The Okuma machining centers are connected to a Fastems quick pallet loading systems, allowing machines to continuously run through a wide range of batch sizes. This mean the plant can stay operational with very few workers on hand and can turn out products on weekends and holidays.
Virtually every step of the production process is found under Oguchi plant’s roof. From raw materials input to final assembly and inspection, Okuma has found a way to maximize their efficiency in production. The biggest influencing factor that helps the company achieve this is assembly complete units at individual stations. Components of production are brought to each assembly station when needed. Okuma machines require much attention to detail and specialized work making an assembly line format of production actually less useful.
Okuma has built a whole new production software management system. It gives operation controllers and managers real time information about product completion and coordinates plant floor workers to bring all the necessary product components to the right assembly station at the right time. It also gives full inventory analysis, product delivery schedules and volume number analysis, and warehouse stock levels. The system also helps integrate the energy savings from environmentally friendly lighting and solar panels into the power used to control automation throughout the facility.