A Look at the Different Types of Fieldbus Cables and How They Impact Industrial Automation
19 May, 2021 | Manufacturing, Industrial Manufacturing, Industrial Automation, Fieldbus Cables
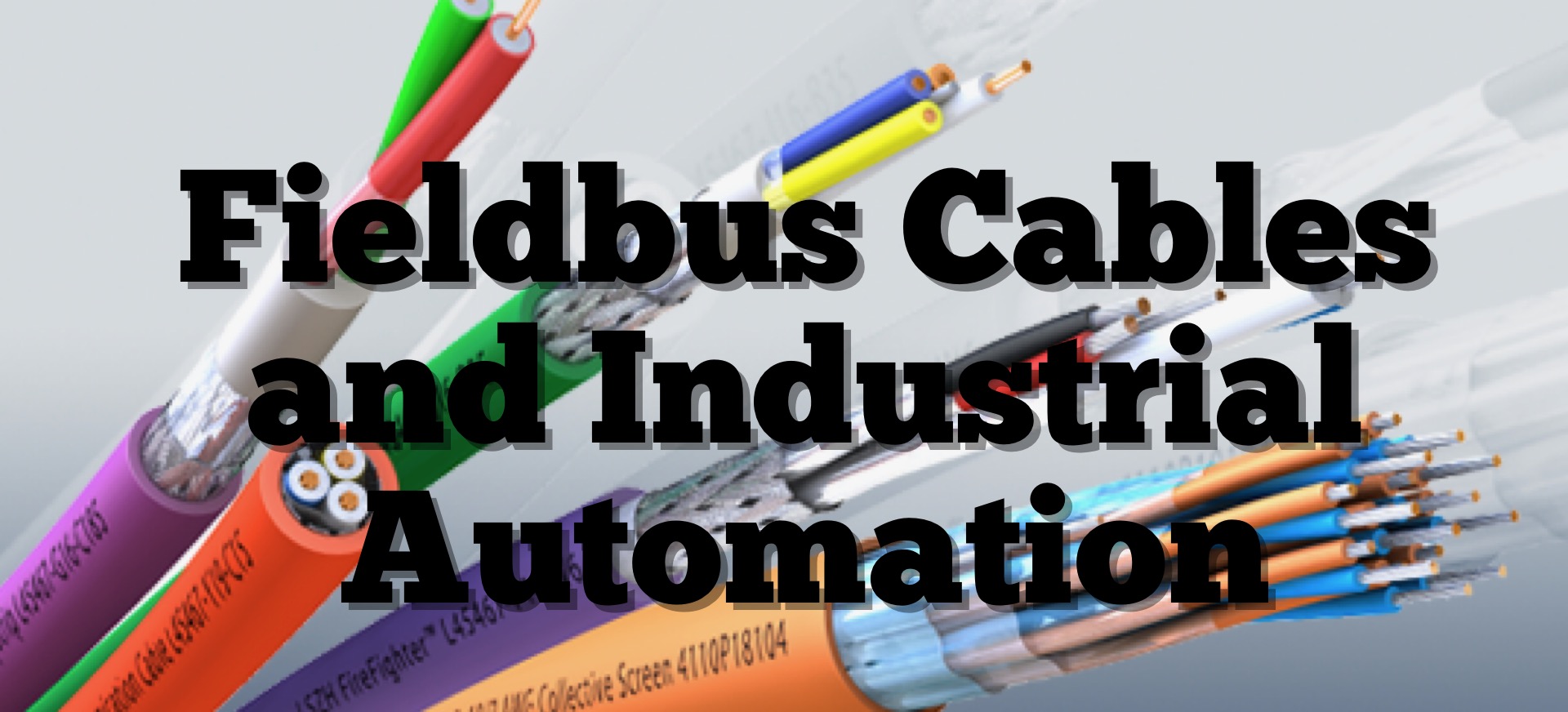
Although Fieldbus might not get as much attention as other parts of the industrial automation process, it is a crucial component. Without it, factories and other industrial facilities wouldn’t be able to operate.
However, Fieldbus systems are not one and the same. Just like the rest of an industrial process, Fieldbus systems must be carefully selected and calibrated to meet the needs of each company that uses them.
Today, the technology behind Fieldbus systems has improved drastically from its early days. This means there are many different types of Fieldbus technology and cables for companies to choose from. Understanding what these types are—and how they are used—is a key part of establishing a highly efficient automated process.

Analog vs. Digital
Fieldbus technology has been around for several decades. In its early days, many companies and inventors scrambled to come up with the best implementation of their technology. This led to a chaotic market and made it difficult for companies to adopt new Fieldbus systems.
Today, Fieldbus technology operates on several standards that dictate key metrics likes its performance and efficiency. Moreover, modern Fieldbus technology must meet standards designed for the industry it is intended to serve. Areas like manufacturing automation, process automation, and building automation all need different types of performance. Modern Fieldbus standards ensure that systems designed for those sectors meet their unique requirements.
Before Fieldbus technology was invented, each device in an automated setup, such as sensors and actuators, needed to be directly connected to its controller with two wires. Today, a single cable, called a “trunk” can connect a large number of devices to one controller. This is possible because the cable delivers segmented “packets” of data to the devices rather than an electric signal. This data is then interpreted by a processor built into the device as well as software running on it.

Types of Fieldbus Cables
Although the specifications of Fieldbus cables can be customized almost infinitely to meet a company’s needs, there are still two main types of Fieldbus trunk in use today. The two are built similarly but have slight differences in the way they operate.
Foundation Fieldbus H1 is the first type of trunk. It features a single twisted pair wire inside an insulated sleeve. This carries both DC power to the devices it connects as well as a digital signal that tells them what to do. It can connect up to 32 devices, including things like pressure transmitters, thermometers, smart valves, actuators, and more, to a distributed control system (DCS).
Profibus PA is another type of trunk that is used frequently in the world of automation. Like the Foundation Fieldbus H1, it is a single twisted pair wire that carries DC power and a digital signal to 32 devices.
The primary difference between the two cables is the interface they run on. For instance, a Foundation Fieldbus H1 system relies on an interface called an H1 card. Meanwhile, a Profibus DP/PA segment coupler is required for the Profibus PA cable.

How Does Fieldbus Expansion Impact Industrial Automation?
As mentioned, Fieldbus technology has come a long way in the past few decades. While early systems often looked like convoluted webs of wires and connections, modern systems are far more streamlined and organized.
With the price of cheap processors becoming more realistic for automation devices, Fieldbus technology will only become more widespread in the years ahead.
For companies that choose to utilize a Fieldbus system, there are many benefits. The most important one is often reduced wiring costs. Since Fieldbus cables can connect to several devices, less wiring is needed to connect an entire system. Meanwhile, Fieldbus systems reduce variability within a company’s processes, help identify issues along automation lines, and improve the reliability of automated systems.
Indramat products such as their servo drives are a great example of how Feildbus cables are put to good use. These cables allow manufacturing costs to be cut as well as cut costs for customers and raise standards in reliability and processing. Here at Wake Industrial we are proud to carry these items, as well as repair items to ensure they are in working order for you!
Moving forward, it will be interesting to see how Fieldbus technology continues to evolve. One thing is certain, however. Fieldbus technology will drive the industrial automation industry forward with every new breakthrough and improvement.