Preparing your secure checkout page...
Warranty
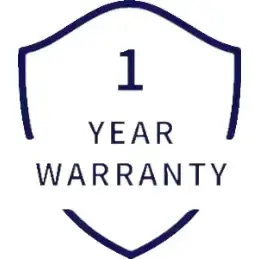
Wake Industrial Warranty
To Speak to a sales representative for pricing and lead time:
Product Description
The AKD-P01206-NBEI-0000 Kollmorgen Ethernet servo drive must be linked with a computer for proper communication. This servo drive highlights the o1 code on its display when it operates normally in velocity mode without any faults. The product has two rotary switches that are used to set the IP address. This device uses the 00 setting for the rotary switch to set the DHCP/AutoIP address. The unit allows only one user to connect to it at a time. Its AKD setup wizard features step-by-step instructions for its first time configuration. This drive is likely to get damaged due to a wrong wiring connection.
The product has a leakage current of more than 3.5 mA to its protective earth connection. This device must incorporate a PLC to monitor its status and acknowledge critical situations. The unit connection should be done using cables that adhere to IEC 60204 specifications and in accordance with the wiring diagram. Its installation and wiring should be executed only when there is no active power connection to the drive. This drive has a switching frequency of 10 kHz of the output stage. The product needs to be associated with UL and CSA Listed 600 VAC, 200 kA Class J time delay cartridge fuses.
This device supports the use of a motor cable with a maximum length of 50 m and 1.5 mm2 cross-section when a choke is used. The unit features a DC bus capacitance of 940µF. Its X10 connector is used to connect the motor feedback. This drive has a unique IP address that helps in its identification on the network. The product has no support for the inclusion of an SD card. This device comes equipped with a direct DC input.