Preparing your secure checkout page...
Warranty
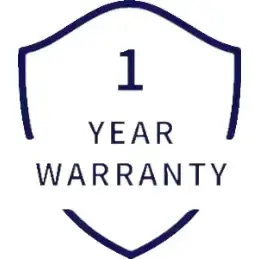
Wake Industrial Warranty
To Speak to a sales representative for pricing and lead time:
Product Description
Kollmorgen products are known across the globe for their high performance and high efficiency. The AKD-P00607-NBEC-0091 Ethernet servo drive is a servo drive that is intended for industrial automation applications. This drive must be installed on to a conductive panel and connected to the Protective Earth ground. The product should be configured before operation by using the Setup Wizard of its Workbench software. This device will not have any communication with the associated PC when Workbench is disconnected from the drive. The unit supports the setting of its IP address with the help of its rotary switches. It has two switches that can be set to any value ranging from 00 to 99.
This servo drive should be assigned a static IP address when it is directly connected to a PC. The product has fully monotonic 16-bit resolution for its analog outputs. This device has an AC rated supply input frequency of 50 Hz to 400 Hz with a tolerance limit of +/-5%. The unit has to be used in combination with a motor choke if the related motor cable has a length of more than 25 meters. It comes integrated with an advanced dynamic braking mode. This drive also houses an internal regen resistor with 33 Ohms rating. The product should be equipped with a constant 24 V supply throughout its operation.
This device supports ambient operation at a maximum temperature of 40 °C. The unit behavior is based on the fault type and the setting of various parameters. Its connected motor can be brought to a controlled stop by configuring one of its digital inputs. This drive does not have the ability to accommodate a vertical load when its Safe Torque Off function is active. The product can cause risk of electrical shock if it is not EMC-grounded properly.