Danaher
Originally an investment trust for real estate, Danaher was founded by Stephen and Mitchell Rales in 1969.
It was based on the Japanese ideology of kaizen; involving processes which motivate continual advancement and improvement. By using this philosophy, Danaher has become one of the leading automation companies in science and technology around the world. It has applied modern day automation to complex environmental and medical issues, enabling huge leaps in dentistry, manufacturing demand solutions, and medical diagnostics. Danahers main focus is to use their automation technology to crack lifes most challenging obstacles in an effort to help the greater good.
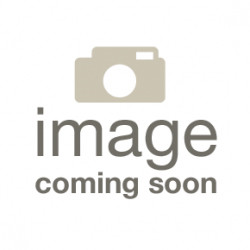