Preparing your secure checkout page...
Warranty
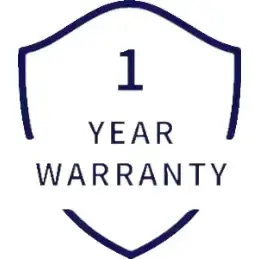
Wake Industrial Warranty
To Speak to a sales representative for pricing and lead time:
Product Description
AM3054-1K40-0000 is a synchronous servo motor. Beckhoff Automation produces the motor for industrial use. In conjunction with a servo drive, the motor forms an ideal solution for applications with requirements for closed loop control. A multi turn encoder installed on the motor provides precise position and speed feedback. The encoder can track the motor shaft position across multiple complete revolutions. The BISS interface on the encoder enhances the overall performance and ensures accurate and efficient operation. The main shaft on the AM3054-1K40-0000 motor includes a feather key and groove. This type of shaft is used to transmit torque and rotational motion to an attached component. The arrangement ensures that the component remains fixed to the shaft while allowing for axial movement along the length of shaft.
Beckhoff recommends -25 to 70 degrees temperature and 5 to 95% humidity for motor transport. Only qualified personnel should handle motor transport. The motor must be protected from hard impacts, especially at the shaft. Maintenance and cleaning of the AM3054-1K40-0000 must also be performed only by qualified personnel. Ball bearings on the motor have a grease filling. They have a 20,000 hour service life and should be replaced after this threshold is crossed when operating under normal rated conditions. Furthermore, the motor should be monitored for bearing noise. Beckhoff recommends checking for bearing noise after every 2500 hours of operation. A name plate is attached to each AM3000 series motor. It provides a means of easy motor identification. The servo motor has a hosing made of die cast aluminum with IP54 protection rating. It supports flange mounting in multiple configurations, including IM V1, IM V3 and IM B5.